Anyone who has spent many years hunting or at the shooting range knows that not every technological novelty in the area of target optics is actually an improvement. For example, very high zoom factors which quickly result in a shadow ring around the edge of the field of view are of little help when it comes to comfortably having an immediate vibrant image. As far as constantly good shooting accuracy is concerned, one constructive feature of the latest generation of scopes also has a dark side. We are talking here about placing the reticle in the second focal plane. It was originally introduced to deliver a fine reticle, even at high magnification. A further reason for the shift over to reticles in the second focal plane was the rise of illuminated reticles, even for daytime use. It was not possible to build a light element small enough to work in the first focal plane. This comes with a price: the disadvantage of a possible shifting of the point of impact as the magnification changes. By contrast, when scopes have reticles in the first focal plane, the point of impact cannot shift as the magnification is changed. That is because the reticle and target image are united before the moving parts that change the magnification come into play. Because of this reliable design, reticles in the first focal plane were almost always the rule in premium European scopes, a rule that still applies today for a few expensive, special-purpose scopes.
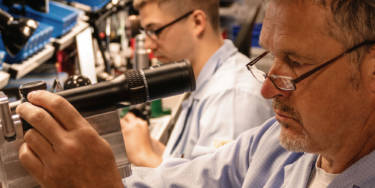
Scope Manufacture
“Attention to detail has a lot to do with personal engagement. That is one of the benefits of manufacturing work.”
Blaser did not want to be satisfied with the second-best solution. Innovative Swiss diffraction grating technology makes it possible – even in the first focal plane – to have a very fine, daylight-rated illuminated reticle. The goal of an absolutely constant point of impact at any magnification is thereby achieved.
Since hunting scopes are frequently subject to very rough conditions, the robustness of the design as a whole was of paramount importance to Blaser engineers. If you pick up one of these scopes, you can see and feel the tough surface coating and the extraordinarily robust, non-slip operating elements. Of special note is the massive, solid metal construction of the reticle adjustment in each turret. This is a new feature for today’s scopes. Precise as a Swiss watch and absolutely repeatable even after thousands of cycles, this alone is proof of the endeavor to achieve constantly uniform shooting accuracy.
It should also go without saying that Blaser didn’t want to compromise when it comes to the optical qualities of its glass. Its transmission, colour fidelity, contrast and imaging performance are the best the market has to offer.
Above and beyond all this, Blaser scopes have features never before seen to this extent: quick reticle adjustment with locking features where the rifle is zeroed at 100 meters, and RZR (recommended zeroing range) with an impact 4 cm high at 100 meters as standard equipment. Parallax adjustment with a detent stop for the most-frequently encountered range of 100 meter is now also standard equipment. Once you have stepped into the Blaser scope production halls in the historic optical town of Wetzlar, you immediately sense the care and passion put into the work here. Entering into competition with the best in the business is a very special challenge for each of the experienced optical technicians working here. Thanks to their new ideas, it has been possible for them to achieve the highest marks in several areas of expertise, proudly upholding the Wetzlar name with full honors.